Vortex Cooling Packing
API 618 Compliant
Cook Compression Vortex Cooling® packing – the only cooled packing case design fully compliant with API 618, 5th edition – significantly improves heat transfer, resulting in extended sealing component life.
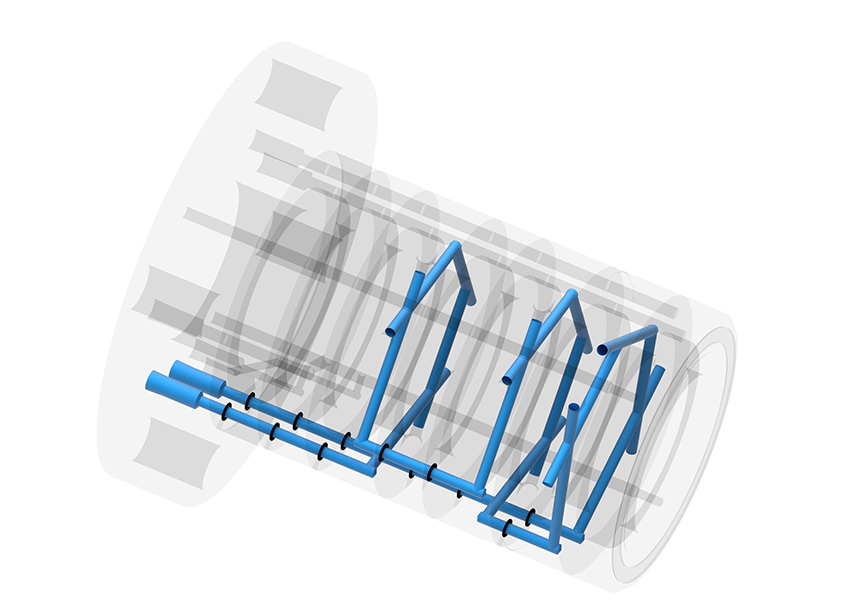
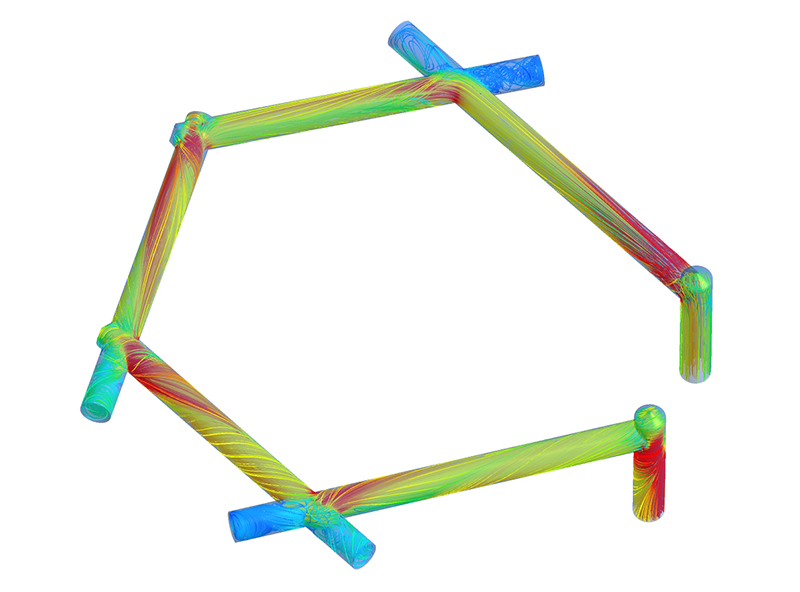
Superior Heat Transfer
Vortex Cooling packing features single-piece cups with tangential coolant channels. The tangential configuration of the coolant channels creates turbulent flow and higher coolant velocity, virtually eliminating dead space. The entire volume of coolant passes through a single, continuous cooling channel from inlet to outlet, resulting in superior heat transfer.
The Vortex Cooling packing case complies with API 618, unlike the “plate and channel” design currently used in moderate- to high-pressure applications.
Reduced Leakage
The Cook Vortex Cooling design may be used in place of conventional pressed-fit coolant cups, which have the potential for gas-to-coolant leakage at higher pressures. The single-piece construction of the Vortex Cooling cup eliminates that leakage. The design also has no rod-encircling O-rings to hamper maintenance.
Improved Clean-out
The straight, tangential cooling channels in Vortex Cooling cases offer superior accessibility through exterior cleaning ports for easy removal of blockage. Even the hardest deposits can be removed quickly with a hand drill.
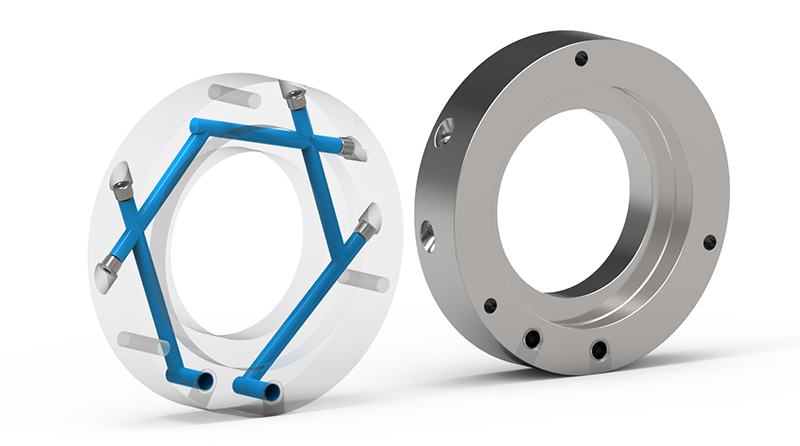
Advantages
- Fully compliant with API 618, 5th edition
- Cooler operation extends sealing component life
- Most efficient heat transfer
- Eliminates gas-to-coolant leakage
- Simplifies installation and maintenance
- Easy access for clean-out
Related Case Study
Packing Upgrade Extends Service Life, Reduces Vent Leakage
Operators were searching for ways to increase rod packing life and reduce seal leakage in a lubricated compressor in hydrogen service. After a field inspection, the Cook team proposed a comprehensive packing upgrade that has achieved more than 18 months of continuous run time and gas vent leakage near zero scfm.
Downloads
Additional Resources
- Cooled Packing Cases: Where Turbulence Is An Advantage (Gas Compression Magazine, April 2018)