Case Study
Breakthrough Materials Expand the Operating Limits of Traditional Hydrogen Compressors
The demand for affordable, cleaner energy sources has presented both opportunities and challenges for equipment manufacturers. Hydrogen is expected to play a crucial role in a variety of uses from transportation to power generation, and governments worldwide are investing in research and infrastructure for the hydrogen economy. However, its success hinges on a new generation of critical machinery and advanced components that can operate beyond historical limitations.
A leading Original Equipment Manufacturer (OEM) with expertise across the hydrogen value chain, including reciprocating compressor technology, recently took on the challenge of designing a compressor capable of operating in the high-pressure, non-lubricated environment required for hydrogen storage and mobility applications. They turned to Cook Compression for assistance.
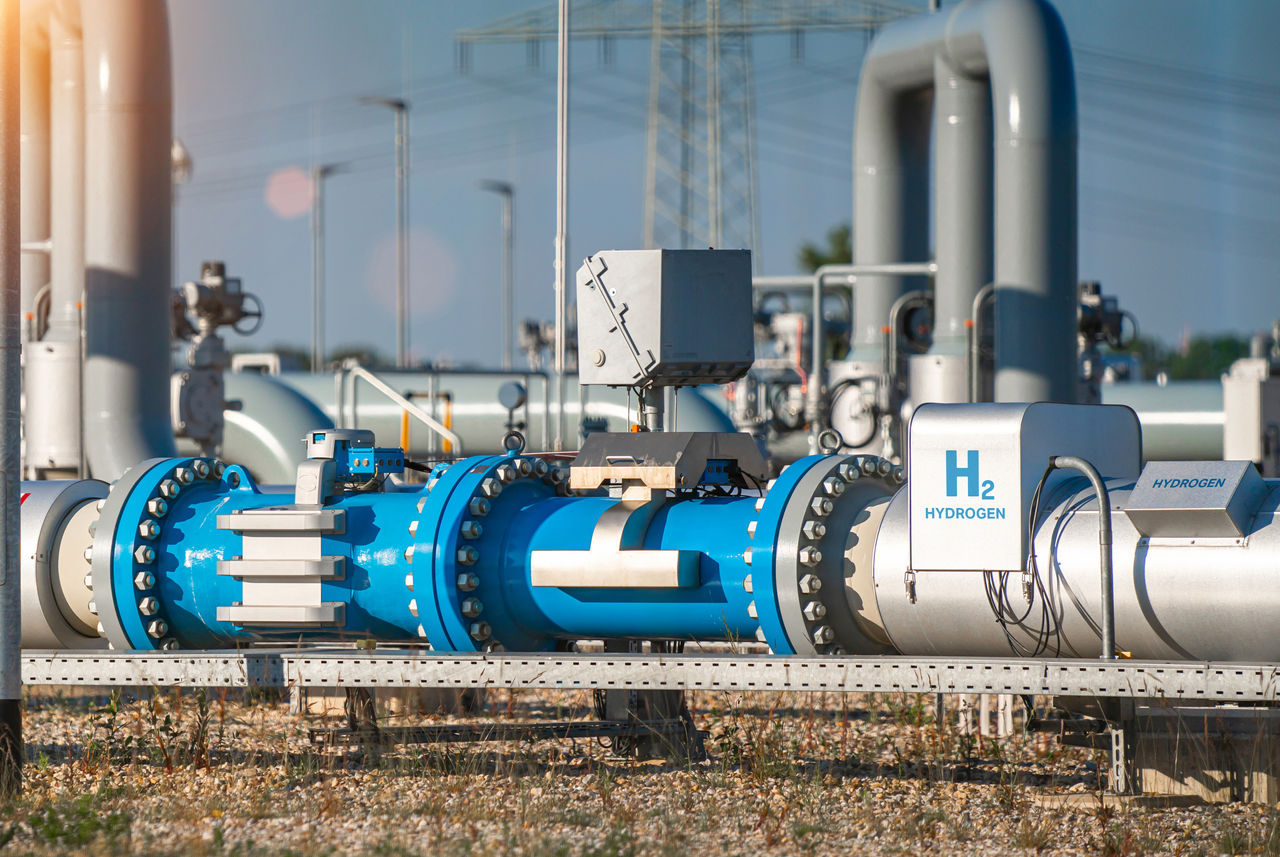
Cook Compression Rethinks Sealing Systems
Cook Compression engineers and materials scientists collaborated with the OEM’s product development team to develop sealing components that minimize hydrogen gas leakage. They soon realized that this task would require a rethinking of sealing systems, including specific ring geometries and an integrated approach for component materials to perform at higher pressures.
Leveraging its experience in creating solutions for optimizing compressor performance, Cook Compression designed specialized proprietary piston rings with innovative geometries to create complicated flow passages that prevent leakage. To prevent excessive or premature degradation, the rings were constructed using TruTech® engineered polymers formulated for hydrogen compression.
The sample parts tested at the OEM’s facility showed early success, proving the new ring designs could cope with high-pressure loads. Initial wear rates were low enough to progress to full endurance testing with hydrogen.
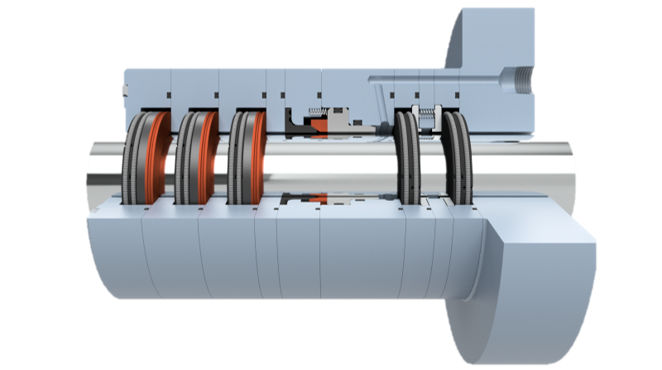
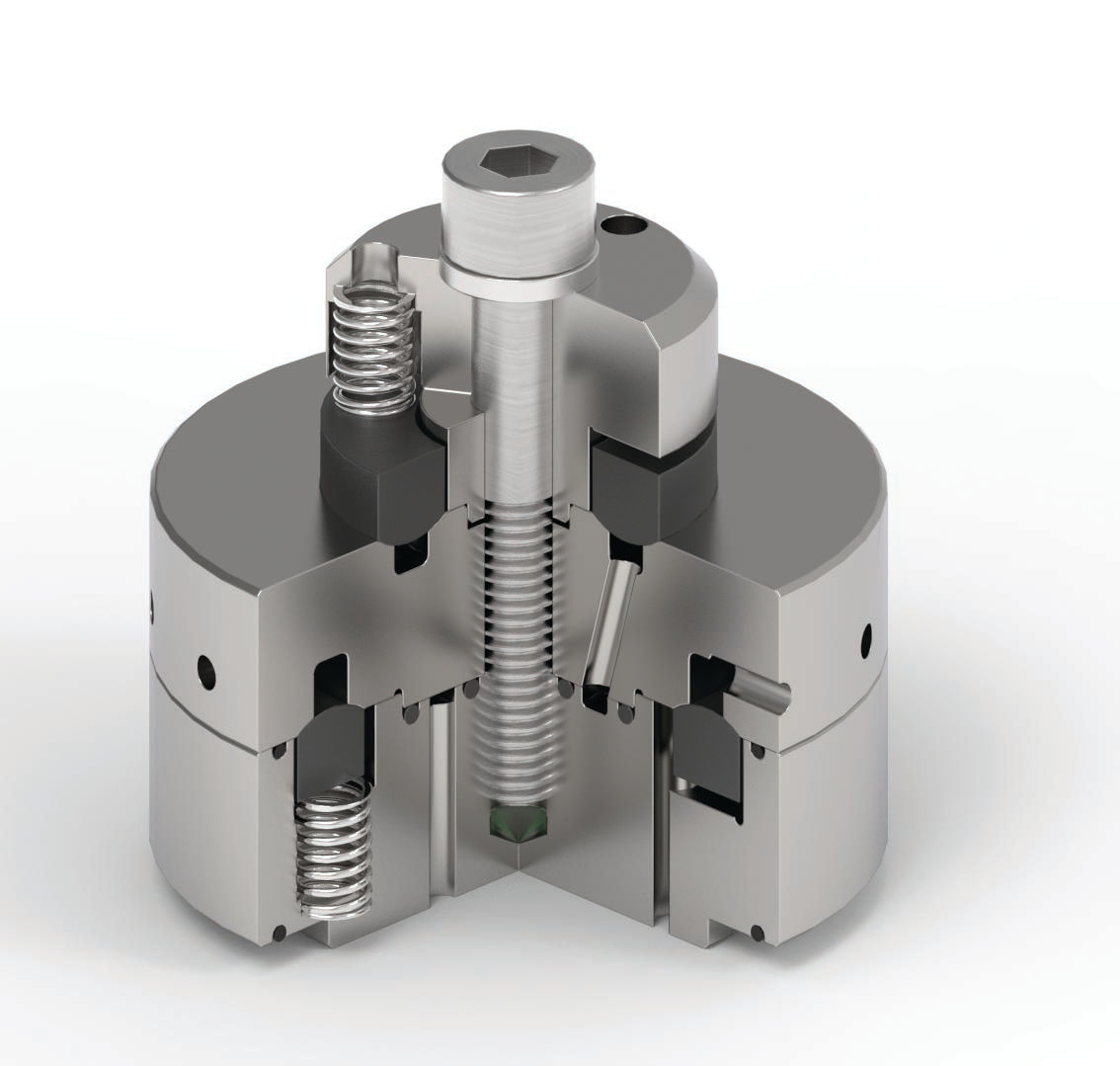
This case study is available to download as a PDF by clicking the button below.
Related Products & Services
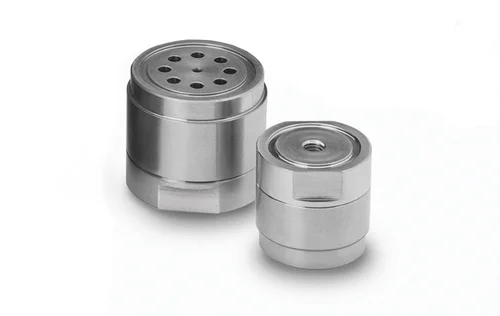